Causes and treatment solutions for leakage of threaded straight joints
Home ✦
Industry Knowledge ✦
Causes and treatment solutions for leakage of threaded straight joints
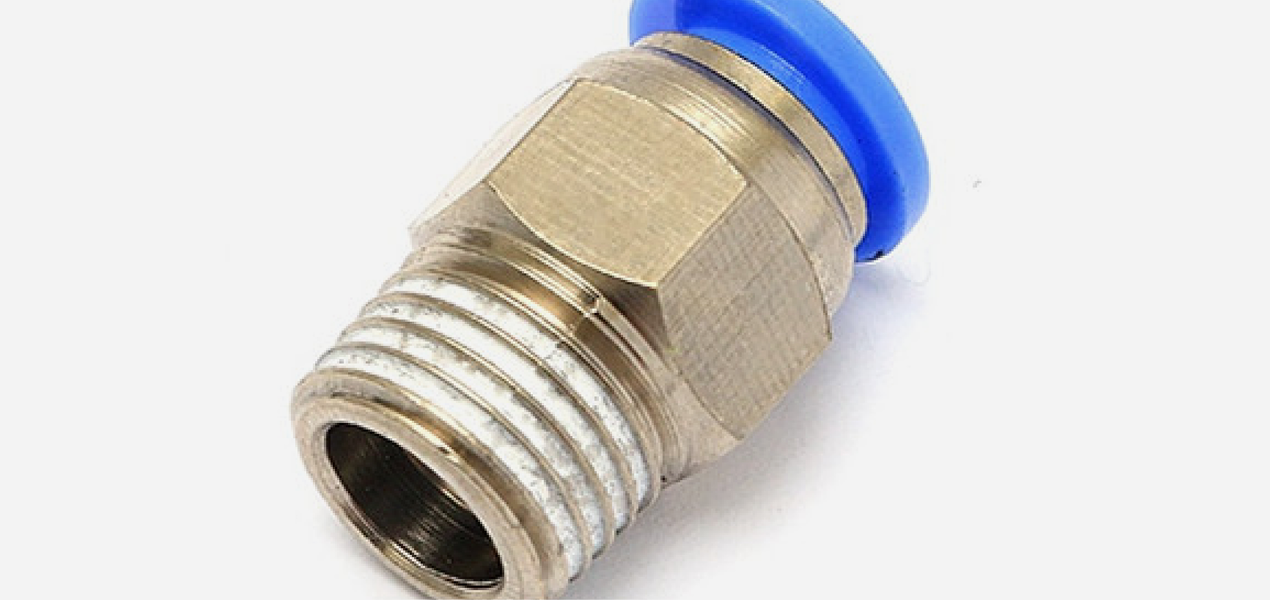
Causes and treatment solutions for leakage of threaded straight joints
Threaded straight-through connectors are commonly used pipe connectors. However, if used improperly or operated improperly, leakage problems are likely to occur. Next, the editor will explain how to avoid leakage problems from two aspects: the cause of leakage and the solution.
1. Causes of leakage
1. Improper installation: If the threaded joint is not installed according to the specifications, leakage problems are likely to occur. The threaded joint should be tightened correctly during installation, and threaded connectors that are too long or too short should not be used.
2. Improper material selection: The leakage of threaded joints is also related to the choice of materials. When purchasing threaded straight-through joints, it is necessary to select appropriate materials based on factors such as the working environment and working pressure, otherwise problems such as rust and deformation will occur, increasing the risk of leakage.
3. Thread damage: The cause of leakage in threaded straight-through joints may also be thread damage. During assembly or use, if the thread is damaged or worn, it will cause leakage.
2. Solution
1. Correct installation: In order to avoid leakage problems, the installation of threaded joints is very important. Perform correct installation operations according to relevant specifications and carefully check the tightness of the threads. If the threads are too loose or too tight, there will be a risk of leakage.
2. Choose high-quality materials: It is equally important to choose high-quality materials. You need to choose high-pressure and corrosion-resistant materials based on factors such as the working environment and working pressure.
3. Replace damaged threads: When the threads are found to be damaged, they need to be replaced in time. When replacing the threads, choose threads with the same material and precision as the original to ensure the integrity of the connection and the normal service life of the joint.
4. Regular maintenance and inspection: Check the connection status of the threaded joints regularly to ensure that the threaded joints are clean, flat, free of rust or other damage. If cracks, deformations, etc. are found, replace the joints in time and replace the necessary sealing gaskets to ensure sealing.
The above are the causes and treatment solutions for leakage of threaded straight-through joints. Therefore, in daily operation, we need to pay special attention to the use of threaded joints, reasonably select materials and operate correctly to ensure their normal operation. During the inspection process, if any problems are found, they need to be dealt with as soon as possible to avoid leakage and other problems.
1. Causes of leakage
1. Improper installation: If the threaded joint is not installed according to the specifications, leakage problems are likely to occur. The threaded joint should be tightened correctly during installation, and threaded connectors that are too long or too short should not be used.
2. Improper material selection: The leakage of threaded joints is also related to the choice of materials. When purchasing threaded straight-through joints, it is necessary to select appropriate materials based on factors such as the working environment and working pressure, otherwise problems such as rust and deformation will occur, increasing the risk of leakage.
3. Thread damage: The cause of leakage in threaded straight-through joints may also be thread damage. During assembly or use, if the thread is damaged or worn, it will cause leakage.
2. Solution
1. Correct installation: In order to avoid leakage problems, the installation of threaded joints is very important. Perform correct installation operations according to relevant specifications and carefully check the tightness of the threads. If the threads are too loose or too tight, there will be a risk of leakage.
2. Choose high-quality materials: It is equally important to choose high-quality materials. You need to choose high-pressure and corrosion-resistant materials based on factors such as the working environment and working pressure.
3. Replace damaged threads: When the threads are found to be damaged, they need to be replaced in time. When replacing the threads, choose threads with the same material and precision as the original to ensure the integrity of the connection and the normal service life of the joint.
4. Regular maintenance and inspection: Check the connection status of the threaded joints regularly to ensure that the threaded joints are clean, flat, free of rust or other damage. If cracks, deformations, etc. are found, replace the joints in time and replace the necessary sealing gaskets to ensure sealing.
The above are the causes and treatment solutions for leakage of threaded straight-through joints. Therefore, in daily operation, we need to pay special attention to the use of threaded joints, reasonably select materials and operate correctly to ensure their normal operation. During the inspection process, if any problems are found, they need to be dealt with as soon as possible to avoid leakage and other problems.