What aspects should be paid attention to when choosing embedded connectors?
Home ✦
Latest News ✦
What aspects should be paid attention to when choosing embedded connectors?
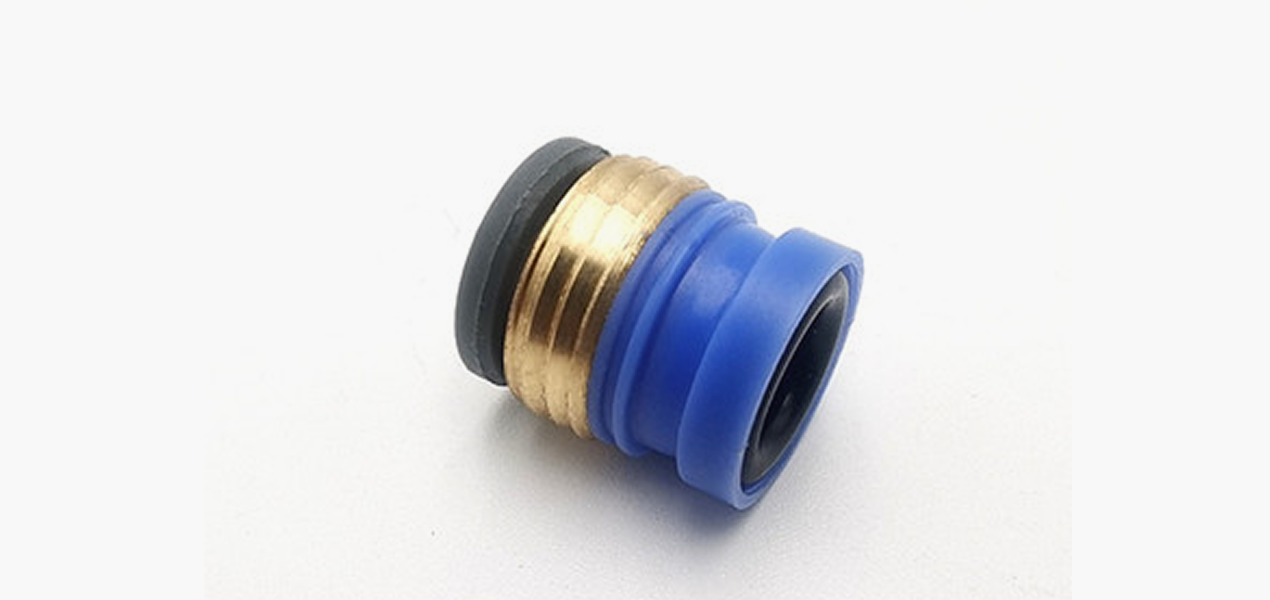
What aspects should be paid attention to when choosing embedded connectors?
With the increasing demand for various pneumatic and air pipe equipment, the use of embedded connectors has increased year by year, playing an increasingly important role in industrial production. When choosing this connector, it is recommended to consider the following aspects, so that the chance of buying the wrong one will be reduced.
1. Material selection
Different materials will affect the durability, corrosion resistance, high temperature resistance and sealing of the joint. Therefore, when choosing a joint, you should choose a material that is suitable for your use environment. For example, some materials are only suitable for use in low temperature environments, while some materials can be used in high temperature environments.
2. Choice of connection method
The connection methods of the joint include vertical insertion, horizontal insertion, flange connection, etc. The specific connection method should be selected according to the actual application scenario and the required connection method.
3. Selection of voltage resistance level
The pressure resistance level of the connector is selected according to the use requirements and pressure. Choosing the wrong level will cause leakage or blockage. Therefore, when purchasing embedded connectors, you must fully understand the pressure of the use environment and the use requirements, and choose the appropriate pressure resistance level.
4. Selection of interface specifications
The interface specifications of connectors produced by different manufacturers are different. Therefore, when choosing, you must fully understand the interface specifications you need and choose connectors that match the required interface specifications.
5. Comparison of performance and size
The joint must not only meet the performance requirements, but also the size must be in line with the working environment and will not affect the matching and installation of surrounding components. When choosing, you should compare and choose according to your actual needs.
With reference to the above aspects, it is very important to choose the right embedded connector. The correct choice can improve production efficiency, reduce costs, and increase the stability and reliability of the production line.
6. Maintainability
When choosing, you also need to consider its maintainability. High-quality joints should be easy to maintain and replace. When choosing, you should choose products that are maintainable and easy to replace to reduce costs and improve efficiency.
Many occasions have high requirements for embedded connectors. Not only do they need to meet the requirements of high performance and high reliability, but users also need to consider the cost and convenience of maintenance. Therefore, it is not easy to choose a satisfactory connector. It is recommended to consider the above aspects when choosing, and I believe you can choose a satisfactory connector.
1. Material selection
Different materials will affect the durability, corrosion resistance, high temperature resistance and sealing of the joint. Therefore, when choosing a joint, you should choose a material that is suitable for your use environment. For example, some materials are only suitable for use in low temperature environments, while some materials can be used in high temperature environments.
2. Choice of connection method
The connection methods of the joint include vertical insertion, horizontal insertion, flange connection, etc. The specific connection method should be selected according to the actual application scenario and the required connection method.
3. Selection of voltage resistance level
The pressure resistance level of the connector is selected according to the use requirements and pressure. Choosing the wrong level will cause leakage or blockage. Therefore, when purchasing embedded connectors, you must fully understand the pressure of the use environment and the use requirements, and choose the appropriate pressure resistance level.
4. Selection of interface specifications
The interface specifications of connectors produced by different manufacturers are different. Therefore, when choosing, you must fully understand the interface specifications you need and choose connectors that match the required interface specifications.
5. Comparison of performance and size
The joint must not only meet the performance requirements, but also the size must be in line with the working environment and will not affect the matching and installation of surrounding components. When choosing, you should compare and choose according to your actual needs.
With reference to the above aspects, it is very important to choose the right embedded connector. The correct choice can improve production efficiency, reduce costs, and increase the stability and reliability of the production line.
6. Maintainability
When choosing, you also need to consider its maintainability. High-quality joints should be easy to maintain and replace. When choosing, you should choose products that are maintainable and easy to replace to reduce costs and improve efficiency.
Many occasions have high requirements for embedded connectors. Not only do they need to meet the requirements of high performance and high reliability, but users also need to consider the cost and convenience of maintenance. Therefore, it is not easy to choose a satisfactory connector. It is recommended to consider the above aspects when choosing, and I believe you can choose a satisfactory connector.